Characteristics of Acrylic and Spandex Fabrics
1. Viscose (Hygroscopic and Easy to Dye)
Manufacturers produce viscose, a man-made cellulose fiber, through solution spinning. Due to the inconsistent solidification rates of the fiber’s core layer and outer layer, it forms a skin-core structure, which is visible in cross-sectional slices. Viscose exhibits the highest hygroscopicity among ordinary chemical fibers, offering excellent dyeability and wearing comfort. However, it has poor elasticity, weak strength, and low wear resistance in wet conditions, making it unsuitable for frequent washing and resulting in poor dimensional stability. Viscose has a high specific gravity, making fabrics heavy, and it resists alkali but not acid.
Manufacturers widely use viscose fibers in various textiles. For example, they use filaments for linings, beautiful silk, flags, ribbons, and tire cords, while short fibers are used for imitation cotton, imitation wool, blending, and interweaving.
2. Polyester (Crisp and Wrinkle-Free)
Polyester features high strength, excellent impact resistance, heat resistance, corrosion resistance, moth resistance, acid resistance (but not alkali resistance), and good light resistance. After 1,000 hours of exposure, it retains 60-70% of its strength. However, it has poor hygroscopicity and is difficult to dye. Polyester fabrics are easy to wash, dry quickly, and maintain good shape, earning them the “wash-and-wear” reputation.
Manufacturers often use polyester filaments as low-elastic yarns to produce various textiles. They blend polyester staple fibers with cotton, wool, and linen for diverse applications. In industrial settings, polyester is used for tire cords, fishing nets, ropes, filter cloths, and insulation materials. Polyester is currently the most widely produced chemical fiber.
3. Nylon (Strong and Wear-Resistant)
Nylon’s greatest advantage is its strength and wear resistance, making it the best in these aspects. It has low density, resulting in lightweight fabrics, excellent elasticity, fatigue damage resistance, and good chemical stability, particularly alkali resistance (but not acid resistance).
However, nylon has poor sunlight resistance. Prolonged exposure causes the fabric to yellow and lose strength. Its moisture absorption is also low, though better than acrylic and polyester.
Manufacturers use nylon filaments extensively in knitting and silk industries. They blend nylon staple fibers with wool or wool-type chemical fibers to produce fabrics like gabardine and vanidine. Industrially, nylon is used for cords, fishing nets, carpets, ropes, conveyor belts, and screens.
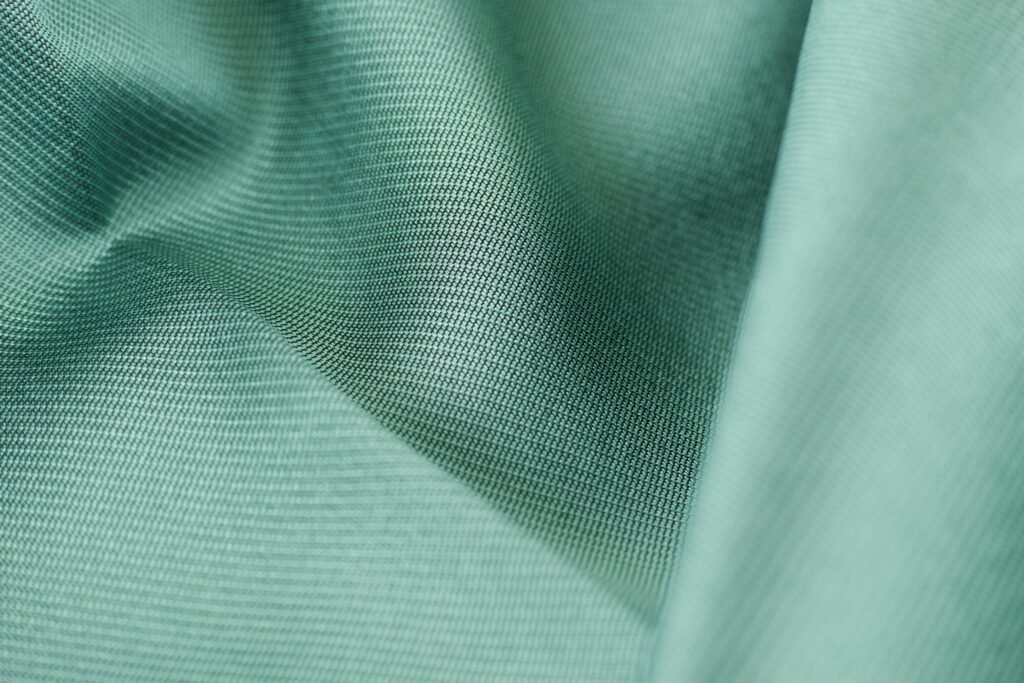
4. Acrylic (Bulky and Sun-Resistant)
Acrylic fiber closely resembles wool in performance, earning it the nickname “synthetic wool.” Its unique molecular structure features an irregular spiral conformation without strict crystallization zones, but with high-order and low-order arrangements. This structure gives acrylic excellent thermal elasticity, allowing manufacturers to process it into bulked yarn. Acrylic has low density, making fabrics lighter than wool, and provides good warmth retention.
Acrylic offers excellent sunlight and weather resistance, ranking first among synthetic fibers. However, it has poor moisture absorption and is difficult to dye. Pure acrylonitrile fiber has a tight internal structure and poor wearing performance, so manufacturers improve its properties by adding second and third monomers. The second monomer enhances elasticity and feel, while the third monomer improves dyeability.
Manufacturers primarily use acrylic for civilian purposes, spinning it purely or blending it to create woolen materials, wool yarn, blankets, sportswear, artificial fur, plush, bulked yarn, hoses, and parasol cloth.
5. Vinylon (Water-Soluble Hygroscopic)
Vinylon’s standout feature is its high hygroscopicity, the best among synthetic fibers, earning it the title of “synthetic cotton.” However, its strength is inferior to nylon and polyester. It exhibits good chemical stability but is not resistant to strong acids and alkalis. Vinylon also has excellent sunlight and weather resistance but performs poorly under wet heat. It has the worst shrinkage elasticity, causing fabrics to wrinkle easily, and its dyeability is poor, resulting in dull colors.
Manufacturers often blend vinylon with cotton to produce fine cloth, poplin, corduroy, underwear, canvas, waterproof cloth, packaging materials, and work clothes.
6. Polypropylene (Lightweight and Warm)
Polypropylene fiber is the lightest among common chemical fibers. It hardly absorbs moisture but has excellent wicking ability. It offers high strength, stable fabric dimensions, good wear resistance, and elasticity, along with excellent chemical stability. However, it has poor thermal stability, is not resistant to sunlight, and is prone to aging and brittleness.
Manufacturers use polypropylene to weave socks, mosquito nets, quilts, thermal padding, diapers, and more. Industrially, it is used for carpets, fishing nets, canvas, water hoses, medical belts, and as a replacement for cotton gauze in sanitary products.
7. Spandex (Elastic Fiber)
Spandex boasts the best elasticity among fibers but has the lowest strength. It has poor moisture absorption but excellent light resistance, acid resistance, alkali resistance, and wear resistance.
Manufacturers widely use spandex in textiles such as underwear, women’s lingerie, casual wear, sportswear, socks, pantyhose, bandages, and medical applications. Spandex is essential for high-performance clothing that prioritizes dynamic and convenient wear. It can stretch 5-7 times its original size, providing comfort, a soft touch, and wrinkle-free properties, ensuring garments maintain their original shape.