Synthetic Fiber
Introduction to Synthetic Fibers
Synthetic fibers represent a groundbreaking category of chemical fibers. Manufacturers synthesize small molecular organic compounds into linear organic polymers, such as polyacrylonitrile, polyester, and polyamide, through addition or condensation polymerization to produce these fibers. Beyond the general advantages of chemical fibers—such as high strength, lightweight, easy care, excellent elasticity, and resistance to mildew—each type of synthetic fiber boasts unique properties that set it apart.
The synthetic fiber industry began its journey in the early 1940s, with polyamide fiber (nylon) becoming the first to achieve industrial production. Shortly after, acrylic and polyester fibers followed. Thanks to their superior performance and abundant raw materials, synthetic fibers have rapidly grown in prominence. In just a few decades, global synthetic fiber production has nearly matched that of natural fibers, becoming a cornerstone of the textile industry. By 1996, global synthetic fiber production reached 19 million tons, with China contributing 2.91 million tons.
Classification of Synthetic Fibers
Synthetic fibers primarily serve the textile industry, and we can categorize them in several ways:
By Application:
- Industrial use
- Civilian use
By Source:
- Natural fibers: Cotton, wool, silk, linen, etc.
- Chemical fibers:
- Artificial fibers: Manufacturers produce these by chemically processing natural cellulose (e.g., wood, cotton lint), such as rayon and artificial cotton.
- Synthetic fibers: Manufacturers make these from petroleum and natural gas-derived polymers, such as polyester and nylon.
By Chemical Composition:
- Polyamide fiber (nylon)
- Polyester fiber
- Polyacrylonitrile fiber (acrylic)
- Polypropylene fiber
- Polyvinyl alcohol fiber (vinylon)
- Polyvinyl chloride fiber (chlorofiber)
Common Synthetic Fibers and Their Applications
1. Polyester
Polyester, scientifically known as polyethylene terephthalate fiber, entered industrial production in the United States in 1953 under the trade name “Dacron.” Since then, it has become a staple in the textile industry due to its versatility and performance.
Production Methods:
- Ester Exchange Method: Manufacturers still use this method today because of its mild reaction conditions and ease of operation, despite its multiple production steps.
- Direct Esterification Method: This streamlined process requires fewer steps and yields higher-quality products but demands more advanced equipment and precise control.
Properties and Uses:
- Strength: Polyester is nearly twice as strong as cotton and three times stronger than wool, making it highly durable.
- Heat Resistance: It performs well in temperatures ranging from 70°C to 170°C, offering the best heat resistance among synthetic fibers.
- Elasticity: Its elasticity rivals that of wool, with superior wrinkle resistance and shape retention.
- Abrasion Resistance: Second only to nylon, polyester excels in wear resistance.
- Water Absorption: While its low moisture absorption makes it quick-drying, it also leads to static buildup and challenges in dyeing.
As a result, manufacturers widely use polyester in clothing, home textiles, and industrial applications such as conveyor belts, tents, and tire cords.
2. Nylon
Nylon, or polyamide fiber, is renowned for its strength and durability. The most common types are nylon 6 and nylon 66.
Production Process:
Manufacturers produce nylon by polymerizing monomers like caprolactam (for nylon 6) or hexamethylenediamine and adipic acid (for nylon 66). They then spin the resulting polymer into fibers through melt spinning.
Properties and Uses:
- Strength and Wear Resistance: Nylon outperforms natural fibers, making it ideal for ropes, tire cords, and sportswear.
- Elasticity: Its excellent elasticity ensures resistance to deformation and fatigue.
- Moisture Absorption: While better than polyester, nylon still generates static electricity due to its low moisture absorption.
- Heat and Light Resistance: Prolonged exposure to sunlight can weaken nylon, so users need to maintain it carefully.
Consequently, manufacturers widely use nylon in clothing, industrial textiles, and blended fabrics.
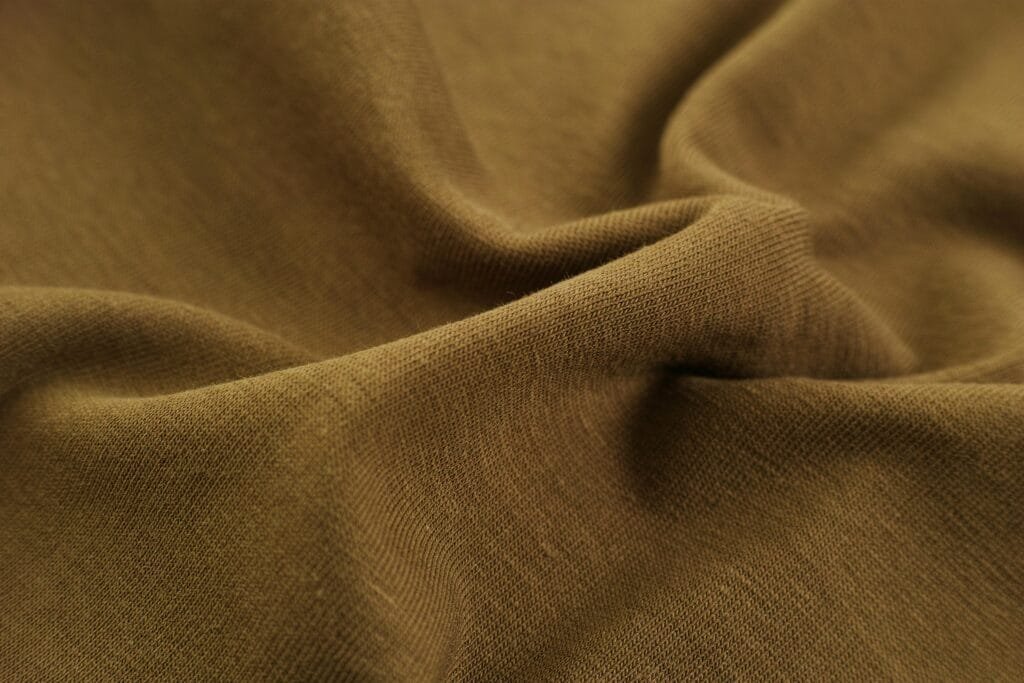
3. Acrylic Fiber
Acrylic fiber, often called “synthetic wool,” mimics the properties of natural wool.
Production Process:
Manufacturers produce acrylic fibers through solution spinning, using propylene as a raw material. They add second and third monomers to enhance softness and dyeability during the process.
Properties and Uses:
- Elasticity: Acrylic fibers offer excellent elasticity, second only to polyester.
- Strength: While not as strong as polyester or nylon, acrylic is significantly stronger than wool.
- Heat and Light Resistance: Acrylic fibers withstand high temperatures and UV exposure better than most synthetic fibers.
Therefore, manufacturers widely use acrylic in sweaters, blankets, and outdoor fabrics.
4. Polypropylene Fiber
Polypropylene fiber, known for its lightweight and cost-effectiveness, is the fourth most produced synthetic fiber globally.
Production Process:
Manufacturers produce polypropylene fibers through solution polymerization, using propylene as the primary raw material.
Properties and Uses:
- Lightweight: Polypropylene is the lightest synthetic fiber, making it ideal for applications requiring low weight.
- Strength and Durability: It rivals polyester and nylon in strength, with excellent abrasion resistance.
- Moisture Absorption: Its low moisture absorption makes it suitable for outdoor and industrial uses.
As a result, manufacturers use polypropylene in carpets, geotextiles, and non-woven fabrics.
5. Vinylon
Vinylon, or polyvinyl alcohol fiber, is celebrated for its high moisture absorption and cotton-like properties.
Production Process:
Manufacturers produce vinylon by polymerizing vinyl acetate and then hydrolyzing it to form polyvinyl alcohol. They treat the fibers with formaldehyde for stability.
Properties and Uses:
- Moisture Absorption: Vinylon absorbs moisture better than most synthetic fibers, making it comfortable for clothing.
- Strength: It is stronger than cotton and highly durable.
- Chemical Resistance: Vinylon resists acids and alkalis, making it suitable for industrial applications.
Thus, manufacturers use vinylon in clothing, canvas, and fishing nets.
6. Chlorofiber
Chlorofiber, or polyvinyl chloride fiber, is known for its flame resistance and chemical stability.
Production Process:
Manufacturers produce chlorofiber by dissolving polyvinyl chloride in solvents and spinning it into fibers.
Properties and Uses:
- Flame Resistance: Chlorofiber is inherently flame-retardant, making it ideal for safety applications.
- Chemical Stability: It resists acids, alkalis, and organic solvents, ensuring durability in harsh environments.
- Moisture Absorption: Chlorofiber has minimal moisture absorption, making it suitable for outdoor and industrial uses.
For these reasons, manufacturers use chlorofiber in protective clothing, industrial filters, and flame-retardant textiles.
Conclusion
In summary, synthetic fibers have revolutionized the textile industry, offering a wide range of properties and applications. From the strength of polyester to the flame resistance of chlorofiber, these materials continue to shape the future of textiles. As technology advances, synthetic fibers will undoubtedly play an even greater role in meeting the demands of modern industries and consumers.
As an important component of chemical fibers, synthetic fibers not only play a significant role in the textile industry but also demonstrate broad application potential in fields such as industry, healthcare, and aerospace. With the advancement of science and technology, researchers and manufacturers are constantly optimizing the production processes and performance of synthetic fibers. In addition, new types of synthetic fibers, such as high-strength and high-modulus fibers, smart fibers, and bio-based synthetic fibers, are gradually emerging, further expanding their range of applications.
Future Development Trends:
- Environmental Protection and Sustainable Development:
As global attention to environmental protection grows, researchers are increasingly focusing on developing bio-based synthetic fibers and degradable synthetic fibers. For instance, polylactic acid (PLA) fiber, a biodegradable synthetic fiber, is steadily replacing traditional petroleum-based fibers. - High-Performance Fibers:
Meanwhile, industries are widely adopting high-strength and high-modulus fibers, such as aramid and ultra-high molecular weight polyethylene fibers, in high-end applications like bulletproof vests, aerospace, and marine engineering. - Smart Fibers:
Similarly, developers are integrating sensing, response, and regulation functions into smart fibers, enabling their use in smart clothing, medical monitoring, and other fields. For example, temperature-controlled fibers can automatically adjust warmth or heat dissipation based on ambient temperature. - Nanofibers:
Furthermore, due to their extremely high specific surface area and unique physical and chemical properties, nanofibers are showing great potential in areas such as filtration materials, biomedicine, and energy storage.
Summary:
In conclusion, synthetic fibers not only serve as the cornerstone of the modern textile industry but also represent a critical direction for future advancements in material science and technological innovation. As environmental awareness grows and technology progresses, researchers and industries are driving breakthroughs in synthetic fibers, thereby enhancing their performance, diversifying their functionalities, and promoting sustainable development. As a result, these advancements are creating more possibilities for improving human life and fostering social development.