What is TPU?
TPU, short for thermoplastic polyurethane elastomer rubber (Thermoplastic polyurethanes in English), is not a traditional textile or leather material. It overcomes many of the shortcomings of PVC, PU leather, and PU coatings, making significant breakthroughs in the application of waterproof and breathable fabrics. TPU combines the best properties of rubber and plastics, offering excellent physical and chemical characteristics. It is a new type of environmentally friendly polymer material that bridges the gap between rubber and plastic, providing both the softness of rubber and the hardness of rigid plastics.
TPU is primarily divided into two types: polyester-based and polyether-based. It features a wide hardness range (60HA-85HD), excellent wear resistance, oil resistance, transparency, and elasticity. These properties make it widely used in daily necessities, sporting goods, toys, decorative materials, and more. Halogen-free flame-retardant TPU can even replace soft PVC, meeting the growing demand for environmentally friendly materials in various industries.
Elastomers, including TPU, are polymer materials with a glass transition temperature below room temperature, elongation at break exceeding 50%, and excellent recovery after deformation. TPU, as a specific type of polyurethane elastomer, offers a broad hardness range and versatile performance, positioning it as a unique material between rubber and plastic. It can be heat-processed and has minimal chemical cross-linking, with its molecules being mostly linear but featuring some physical cross-linking.
Characteristics of TPU
TPU boasts several key characteristics:
- Wide Hardness Range: By adjusting the ratio of its components, manufacturers can produce TPU with varying hardness levels, all while maintaining excellent elasticity and wear resistance. Its elastic modulus ranges from 10 to 1000 MPa, bridging the gap between rubber (1–10 MPa) and rigid plastics (1000–10,000 MPa).
- High Mechanical Strength: TPU products exhibit exceptional load-bearing capacity, impact resistance, and shock absorption.
- Outstanding Cold Resistance: TPU remains flexible and elastic even at temperatures as low as -35°C, performing well across a wide temperature range (-40°C to 120°C) without requiring plasticizers.
- Excellent Processability: Manufacturers can process TPU using common thermoplastic methods such as injection molding, extrusion, and calendering. It can also be blended with other polymers to create alloys with complementary properties.
- Oil, Water, and Mildew Resistance: TPU resists oils, solvents, and mildew, making it suitable for demanding environments.
- Recyclability: TPU is environmentally friendly and can be recycled efficiently.
- Weather and Radiation Resistance: TPU performs well under prolonged exposure to sunlight and high-energy radiation.
Additionally, TPU is known for its exceptional wear resistance, tear strength, flexural strength, high tensile strength, high elongation, and low long-term compression set.
Three Major Properties of TPU
TPU’s properties can be categorized into mechanical, physical, and environmental characteristics:
- Mechanical Properties:
- Hardness: Measured using Shore A or Shore D scales, TPU’s hardness depends on its hard segment content. Higher hardness improves tensile modulus and tear strength but reduces elongation.
- Tensile and Tear Strength: As hardness increases, TPU’s tensile and tear strength improve significantly due to enhanced physical cross-linking.
- Physical Properties:
- TPU maintains excellent elasticity and flexibility across a wide temperature range.
- It resists oils, water, and mildew, making it durable in harsh environments.
- Environmental Properties:
- TPU is recyclable and environmentally friendly.
- It resists weathering and high-energy radiation, ensuring long-term performance.
Applications of TPU
TPU’s versatility makes it suitable for a wide range of industries:
- Automotive Parts: Ball joints, dust covers, brake pedals, door locks, bushings, and shock-absorbing components.
- Industrial Components: Gears, seals, bearings, connectors, and printing rollers.
- Clothing Accessories: Bra straps, elastic bands, and sportswear.
- Footwear: Soles, heels, ski boots, and safety boots.
- Pipes and Hoses: High-pressure, medical, and fuel pipes.
- Films and Sheets: Air cushions, diaphragms, and composite fabrics.
- Wires and Cables: Power cables, automotive wiring, and communication cables.
- Other Uses: Watch straps, conveyor belts, and adhesives.
Market Size and Development Prospects
The global TPU market has grown significantly, driven by industrial demand and environmental regulations. From 2007 to 2010, the market saw a compound annual growth rate (CAGR) of 6.6%, with global consumption reaching 465,500 tons in 2010. By 2015, demand was expected to reach 750,000 tons, with Asia leading the market due to industrial growth in China and Southeast Asia.
In China, TPU production has expanded rapidly, particularly in low-end applications like footwear and machinery. However, high-end products, such as those used in adhesives and films, still rely on imports from Europe and the United States.
New TPU Materials
Recent advancements in TPU technology have introduced innovative materials such as waterproof and breathable membranes, nanofiber diaphragms, and coated fabrics. These materials are not only functional but also aesthetically pleasing, with smooth or textured surfaces and vibrant colors.
TPU composite fabrics are produced through two main methods:
- Post-Lamination: TPU film is first produced and then bonded to fabric.
- Online Lamination: TPU is directly cast onto the fabric, creating a seamless composite material.
Conclusion
TPU is a versatile and environmentally friendly material with applications spanning automotive, industrial, clothing, footwear, and more. Its unique combination of properties—ranging from elasticity and wear resistance to recyclability—makes it a valuable material in modern manufacturing. As technology advances, TPU’s role in various industries will continue to grow, driving innovation and sustainability.
Overall
TPU Composite Fabric: A Versatile Functional Material
TPU composite fabric is a cutting-edge functional material created by combining thermoplastic polyurethane elastomer (TPU) film with various fabrics, such as knitted fabric, polyester, and nylon, through advanced composite processes. This innovative material integrates the exceptional properties of TPU with the unique characteristics of the base fabric, making it highly versatile and widely applicable across multiple industries. Below are its key highlights:
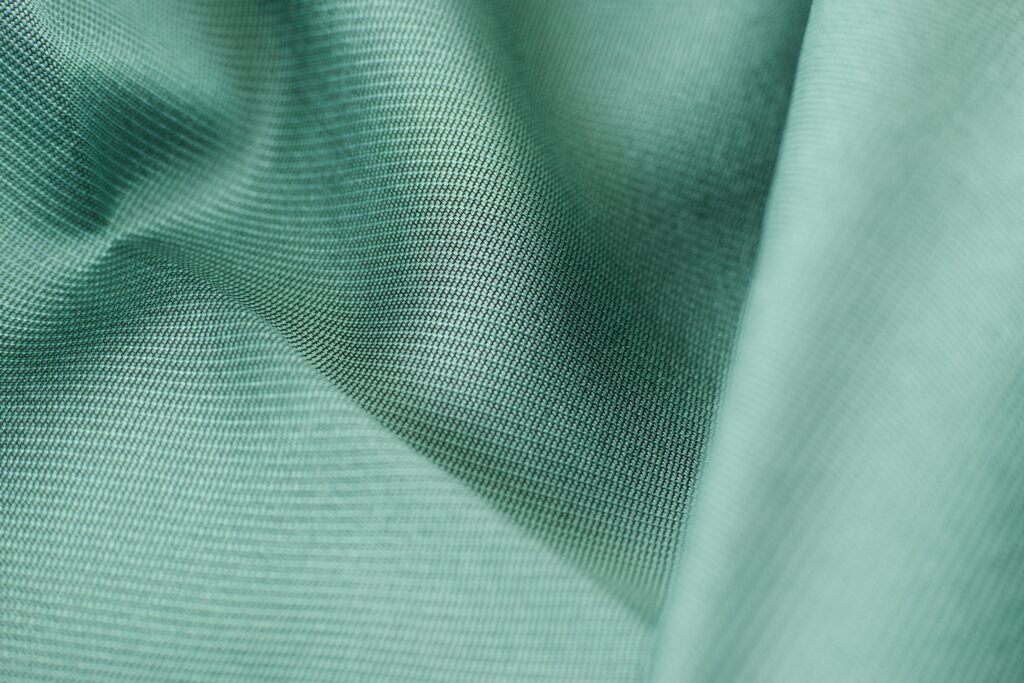
1. Material Composition and Manufacturing Process
- TPU Material Properties:
Manufacturers produce TPU, an eco-friendly polymer material, by reacting polyols with isocyanates. TPU exhibits high elasticity, wear resistance, cold resistance (down to -35°C), oil resistance, hydrolysis resistance, and a broad hardness range. By adjusting formulations, manufacturers can tailor TPU’s performance to meet specific requirements. - Composite Processes:
- Post-attachment Method: Manufacturers first produce TPU film and then bond it to fabric using adhesives or hot-melt glue.
- In-line Compounding: Manufacturers directly coat or calender molten TPU onto fabric, creating an integrated structure.
- Eco-friendly Trend: To address odor issues, manufacturers are transitioning from traditional oil-based adhesives to hot-melt adhesives, enabling greener and odor-free production.
2. Core Properties
- Waterproof & Breathable:
The microporous structure of TPU film blocks liquid water while allowing water vapor to pass through, making it ideal for waterproof clothing, tents, and similar applications. - Mechanical Performance:
TPU composite fabric offers high impact resistance, load-bearing capacity, and shock absorption, making it suitable for sports gear, shoe components, and more. - Weather Resistance:
The material retains elasticity even at -35°C, demonstrating excellent cold resistance. It also resists high temperatures, oxidation, and maintains long-term durability. - Processing Flexibility:
Manufacturers can process TPU composite fabric using injection molding, extrusion, calendering, and other methods. It can also be easily combined with other materials to create functional composites. - Eco-friendliness & Safety:
TPU is non-toxic, recyclable, and some medical-grade variants pass biocompatibility tests. However, manufacturers must ensure proper handling to minimize chemical residues during production.
3. Applications
- Outdoor & Sports:
Manufacturers use TPU composite fabric to produce waterproof backpacks, ski wear, and mountaineering gear, leveraging its windproof, cold-resistant, and breathable properties. - Medical & Hygiene:
The material is ideal for anti-decubitus mattresses and sanitary product backing films, thanks to its waterproof breathability and biocompatibility. - Industrial & Electronics:
Manufacturers use anti-static TPU fabrics for electronic component packaging and automotive manufacturing to prevent electrostatic damage. - Consumer Goods:
TPU composite fabric is widely used in footwear, luggage, and phone cases, benefiting from its abrasion resistance and moldability.
4. Considerations
- Breathability Debate:
While TPU film is theoretically breathable, poor design—such as in some menstrual underwear—may hinder airflow. Manufacturers must evaluate breathability based on specific production techniques. - Potential Risks:
Low-quality TPU may retain harmful substances like isocyanates, which can pose skin allergy risks with prolonged exposure. Consumers should opt for certified products to ensure safety.
Summary
TPU composite fabric combines the functionality of TPU with the versatility of base fabrics, creating a high-performance material with broad applications. Its eco-friendly nature and adaptability make it indispensable in outdoor gear, medical supplies, industrial protection, and consumer goods. However, manufacturers must prioritize production quality and tailor the material to specific use cases to mitigate potential risks and maximize performance.