- Introduction:
Spandex, short for polyurethane fiber, is an elastic fiber typically composed of multiple filaments, usually 10D per filament, with options now including 15D or even 20D per filament. Theoretically, fewer filaments result in better yarn uniformity because there is less chance of overlapping. The production solution DMAC used in dry spinning can harm the human liver. Generally, 10D per filament contains 0.5mg/kg, but 15D per filament exceeds this standard. When producing spandex, manufacturers must pay special attention to winding tension, the number of counts on the drum, breaking strength, breaking elongation, degree of formation, amount of oil adhesion, and elastic recovery rate. These factors directly affect weaving, particularly in the knitting production of single-sided cloth.
- Basic characteristics of spandex
Spandex, which translates to “spandex” in English, is an elastic fiber with the scientific name polyurethane fiber (Polyurethane), abbreviated as (PU). In mainland China, people call it spandex. This fiber exhibits high elasticity, allowing it to stretch 6 to 7 times its original length, but it quickly returns to its initial state once the tension disappears. Its molecular structure consists of a chain-like, soft, and extensible polyurethane, connected with hard segments to enhance its properties. Manufacturers classify elastic fibers into two categories: one is polyester-based, and the other is polyether-based. Polyester elastic fibers offer strong antioxidant and oil-resistant properties, while polyether elastic fibers resist mildew and detergents.
- Advantages of spandex
Spandex has excellent elasticity. The strength is 2 to 3 times higher than that of latex, the line density is also finer, and it is more resistant to chemical degradation. Spandex has good acid and alkali resistance, sweat resistance, seawater resistance, dry cleaning resistance, and wear resistance.
- Brief history of spandex production:
Chemical fibers refer to fibers made from natural or synthetic high polymers and processed by chemical methods. They can be divided into two categories: artificial fibers and synthetic fibers. There are two types of man-made fibers, namely man-made cellulose fibers (such as viscose fibers, strong fibers, etc.) and man-made protein fibers (such as soybean fibers, peanut fibers, etc.), while the camp of synthetic fibers is relatively large, including polyester fibers (i.e. polyester), polyamide fibers (nylon 6, nylon 66, etc.), polyacrylonitrile fibers (acrylic fibers), polyvinyl alcohol formal fibers (vinylon), polypropylene fibers (polypropylene fibers), polyvinyl chloride fibers (chlorofibers), and polyurethane fibers (spandex). The composition contains more than 85% of polyurethane components, and the trade names include Lycra (Lycra, the United States, the United Kingdom, the Netherlands, Canada, Brazil), Neolon (Neolon, Japan), Dorlastan (Dorlastan, Germany), etc.
First, it was successfully researched by Bayer Company in Germany in 1937, and DuPont Company in the United States began industrial production in 1959. It has now sold its spandex industry to Koch Industries in the United States, with a total production capacity of about 100,000 tons. The current global total spandex production capacity is about 600,000 tons, and the spandex production capacity of Hyosung Company in South Korea is close to 120,000 tons, making it the world’s first. The first spandex enterprise in China is Yantai Spandex Factory, which started production in 1989. Mainland China currently has a production capacity of about 350,000 tons, making it the world’s largest spandex producer.
There are two types of spandex, one is a mosaic copolymer of aromatic diisocyanate and polyester segments containing hydroxyl groups (referred to as polyester-type spandex), and the other is a mosaic copolymer of aromatic diisocyanate and polyether segments containing hydroxyl groups (referred to as polyether-type spandex). Spandex fiber, elastic polyolefin fiber and elastic composite fiber are collectively referred to as elastic fiber.
V. Physical properties of spandex
A synthetic fiber with high elongation at break (more than 400%), low modulus and high elastic recovery rate. The Chinese trade name for multi-block polyurethane fiber. Also known as elastic fiber. Spandex has high elongation (500% to 700%), low elastic modulus (200% elongation, 0.04 to 0.12 g/denier) and high elastic recovery rate (200% elongation, 95% to 99%). Except for its high strength, its other physical and mechanical properties are very similar to those of natural latex. It is more resistant to chemical degradation than latex, has moderate thermal stability, and has a softening temperature of about 200°C. Most dyes and finishing agents used for synthetic and natural fibers are also suitable for dyeing and finishing of spandex. Spandex is resistant to sweat, seawater, various dry cleaning agents, and most sunscreens. It will also fade after long-term exposure to sunlight or in chlorine bleach, but the degree of fading varies greatly depending on the type of spandex.
Spandex fiber achieves its high elasticity due to its polymer chain structure, which consists of a low-melting point, amorphous “soft” segment as the matrix and a high-melting point, crystalline “hard” segment embedded within it. The flexible segment molecular chains form a network structure with certain cross-linking, allowing them to stretch freely due to the small interaction force between the chains, resulting in high elongation performance. The rigid segment molecular chains, with their relatively strong binding force, prevent indefinite stretching, giving the fiber high resilience. Most nylon filaments have a dog-bone-shaped cross-section, with some featuring smooth or serrated surfaces. Spandex has the lowest breaking strength among all textile fibers, ranging from 0.44 to 0.88 CN/dtex (polyether types exhibit higher strength than polyester types). Its moisture absorption range is small, typically 0.3-1.2% (multifilament absorbs slightly more moisture than monofilament). Heat resistance varies significantly by variety, with most fibers remaining undamaged when exposed to temperatures between 90~150℃ for short periods. The safe ironing temperature is below 150℃, and it can withstand heated wet washing. Spandex dyes well, adapting to most dye varieties, and the dye exhibits strong affinity for the fiber. It also demonstrates good chemical resistance, standing up to most acids, alkalis, chemicals, organic solvents, dry cleaning agents, and bleaching agents, as well as sunlight and weather conditions. However, it is not resistant to oxides, which can cause the fiber to yellow and lose strength.
Manufacturers rarely use spandex alone, instead blending it in small quantities into fabrics. This fiber combines rubber-like properties with fiber characteristics, often serving as the core yarn in core-spun yarns, known as elastic core-spun yarns. These yarns offer several advantages: first, they provide a good feel and appearance, with the outer natural fibers offering excellent moisture absorption; second, only 1-10% spandex filaments are needed to produce high-quality stretch yarns; third, the elasticity can be controlled within a range of 10% to 20%, allowing for customization based on the product’s intended use. It is easy to spin yarns of varying thicknesses, from 25 to 2500 denier, making it widely used in elastic woven fabrics such as socks, furniture covers, ski suits, sportswear, medical fabrics, belts, military equipment, and the elastic parts of space suits. As consumers demand lighter, more comfortable, and softer fabrics, low-denier spandex fabrics are increasingly dominating synthetic fiber markets. Additionally, spandex bare yarns and twisted yarns, created by twisting spandex with other fibers, are primarily used in various warp knitting, weft knitting, woven fabrics, and elastic textiles.
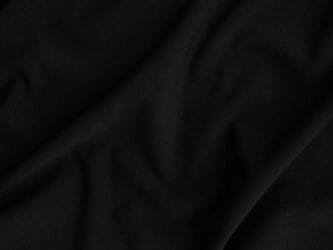
- Production method
Spandex fiber overcomes the quality defects such as stress, strain performance, count range and moldability of rubber yarn.
- Dry spinning
DRY SPINNING, a method in which the solution is solidified into yarn due to the evaporation of the solvent under hot air flow.
Production process: solution—-spinning pump—-drying box, 100℃ hot air blows through to evaporate the solution—-spinning—-winding molding.
Spinning speed: 200~800M/min.
Spinning temperature: 200~230℃.
Fiber fineness: 22.2~1244dtex.
- Melt spinning: A method of heating a polymer to a temperature above its melting point to form a melt and filament.
Production process: polymerize polymer without solvent —- granulate —- slice at a constant temperature —- clean and remove impurities —- dry —- dehydrate —- enter screw press to form melt —- extrude through spinneret —- cool through cold box —- wind up.
Spinning speed: 600~1600M/min.
Spinning temperature: 160~220℃.
Fiber fineness: 9~1100dtex.
Features: short process, low cost, low pollution.
Wet spinning: A method of solidifying a stock solution into filament by double diffusion in a coagulation bath.
Production process: stock solution —- spinning pump —- enter warm water from spinneret, below 90℃ —- regeneration tank coagulation bath —- remove solvent —- filament washing —- drying —- winding up.
Spinning speed: 50~150M/min.
Spinning temperature: warm water below 90℃.
Fiber fineness: 44~440dtex.
Features: This method has high pollution, slow spinning speed and high cost in the production process.
Chemical reaction method
A method in which a polymer is made into a solution and then chemically reacted with a chain extender to solidify into a filament.
Production process: solution—-through a spinneret to a coagulation liquid—-adding a chain extender—winding and forming—-hardening—processing into a mesh fiber.
Spinning speed: 50~150M/min.
Fiber fineness: 44~80dtex.
Features: This method has high pollution and high cost in the production process.
Form
- Spandex production also has different brightness forms, usually:
Transparent, CLEAR-LUSTER: The surface fiber is relatively smooth, so it reflects light and becomes transparent, with low friction rate, poor uniformity of yarn, and poor coloring. It is suitable for production with short fiber materials and is mostly used in warp fabrics.
Dull-LUSTER: It is white, the surface fiber is relatively uneven, the friction surface is large, and the coloring effect is good. It is suitable for production with long fibers and is used for coarse roots, such as bra products and accessories.
Translucent, BRIGHT-LUSTER: Titanium dioxide and anti-slip agents are added inside, which has strong resistance to chemical agents. It is mostly used in swimsuits because of its anti-chlorine function.
Matte, MATT-LUSTER: It is between white and translucent, matte white, suitable for knitting. - Spandex serves various purposes and comes in multiple product forms, primarily divided into three types: bare yarn, core-spun yarn, and covered or twisted yarn. Each combination corresponds to different applications.
- Bare yarn: This is 100% spandex yarn. Manufacturers rarely use bare yarn directly on fabrics. Instead, they typically produce it alongside other materials using specialized equipment. Bare yarn is most commonly used in knitwear, such as swimsuits and sportswear, and usually ranges from 22 to 78 Dtex.
- Core-spun yarn: This yarn consists of bare yarn as the core and other materials as the outer layer, referred to as CSY. When using cotton as the core, manufacturers usually insert the stretched bare yarn into the spinning machine of a ring spinning machine. They must appropriately adjust the elongation of the bare yarn wrapped around the core yarn and suppress its expansion rate to 2-3 times. Today, core yarn is categorized into hard core yarn and soft core yarn. The materials used for the outer layer include cotton, polyester, acrylic, and others. Core-spun yarn is widely used in fabrics, knitwear, bandages, socks, underwear, and jeans, typically ranging from 22 to 235 Dtex.